Understanding Prototype Injection Molds in Metal Fabrication
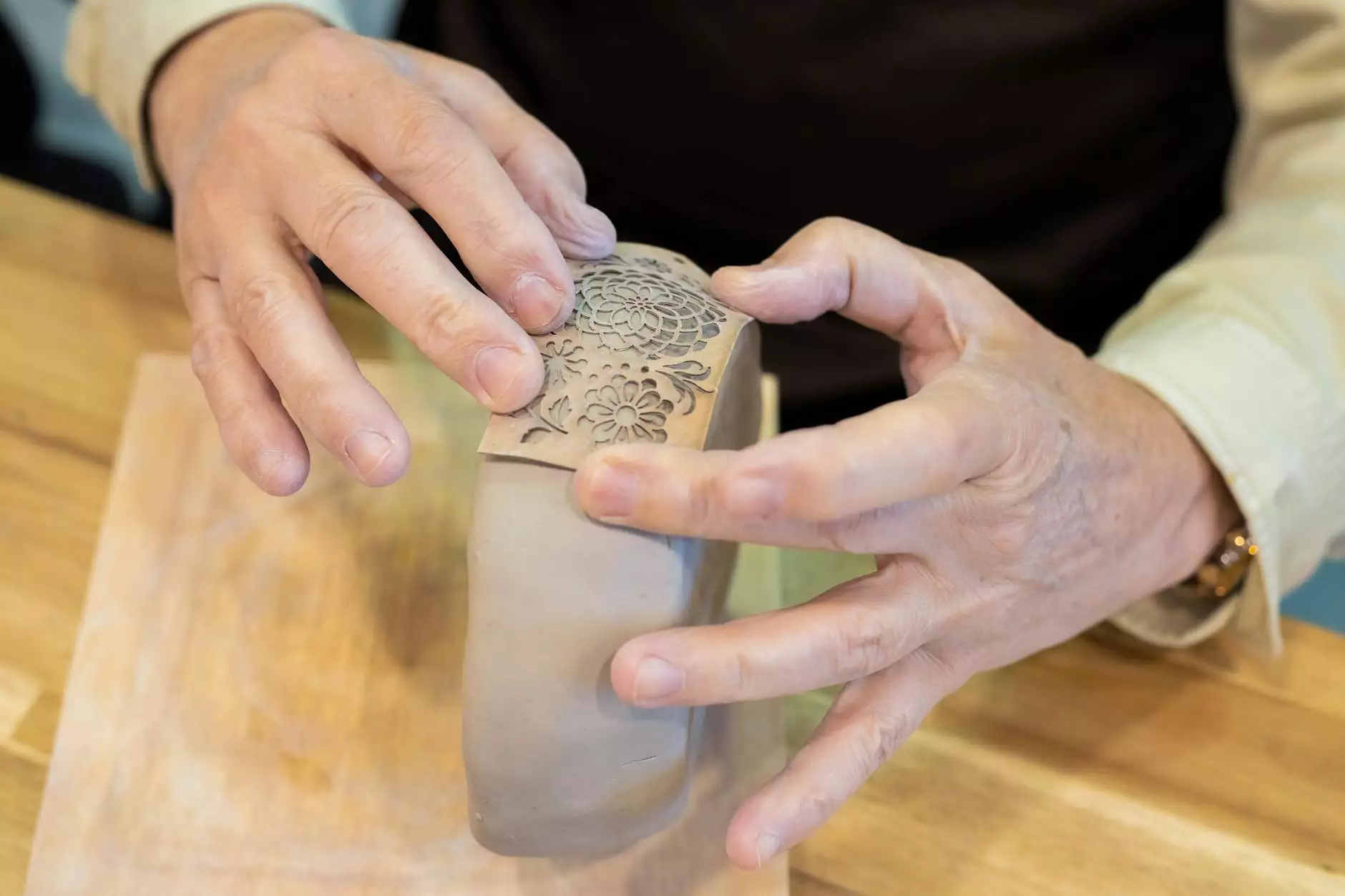
What Are Prototype Injection Molds?
Prototype injection molds are specialized tools used in the manufacturing process to create prototype components through injection molding. These molds are designed to produce near-identical copies of a product with remarkable precision, allowing companies to validate their designs before mass production.
The Importance of Prototype Injection Molds
In the highly competitive world of manufacturing, speed and accuracy are paramount. The importance of prototype injection molds cannot be overstated; they serve as a bridge between concept and production, enabling businesses to:
- Test and refine design concepts quickly.
- Reduce time-to-market for products.
- Minimize costs associated with full production runs.
- Improve product quality through iterative testing.
How Prototype Injection Molds Work
Prototype injection molding involves several key steps:
- Design: Engineers create a CAD model of the desired part.
- Mold fabrication: The mold is manufactured, typically from aluminum or steel, depending on the required durability.
- Injection: Plastic material is injected into the mold under high pressure.
- Cooling: The material cools and solidifies to take the shape of the mold.
- Demolding: The finished part is ejected from the mold for inspection and testing.
Benefits of Using Prototype Injection Molds
Utilizing prototype injection molds provides several advantages to businesses, including:
- Cost Efficiency: Lower production costs for small batch runs compared to traditional methods.
- Quick Turnaround: Rapid prototyping allows for fast adjustments and modifications.
- High Precision: Manufacturing accurate components that meet strict specifications.
- Material Variety: Capability to test different materials and designs in the production phase.
Applications of Prototype Injection Molds
The applications of prototype injection molds span various industries:
- Automotive: Parts prototyping for vehicles such as dashboards, trim, and housings.
- Consumer Electronics: Enclosures and components for smartphones, tablets, and other devices.
- Medical Devices: Development of intricate components essential for medical equipment.
- Food Packaging: Prototyping containers and packaging solutions that adhere to safety standards.
- Toys: Designing and producing prototypes for ensuring safety and playability.
Choosing the Right Fabricator for Your Prototype Injection Molds
Selecting the appropriate fabricator for your prototype injection molds is critical. Here are some factors to consider:
- Experience: Look for a company with a proven track record in prototyping and injection molding.
- Technology: Ensure they utilize modern equipment and software to create molds.
- Material Options: A wide range of material capabilities can enhance design flexibility.
- Customer Support: Opt for a provider that offers strong support throughout the prototyping process.
- Lead Times: Fast turnaround times can be crucial in getting your product to market.
Case Studies: Successful Implementation of Prototype Injection Molds
Case Study 1: Automotive Component Development
A leading automotive manufacturer faced time constraints in launching a new vehicle model. By employing prototype injection molds, they produced test parts in just a few weeks. This accelerated process allowed for immediate design modifications, ensuring that the final product met consumer expectations.
Case Study 2: Medical Device Innovation
A medical device startup utilized prototype injection molds to create a complex sensor housing. Through rapid prototyping, they identified design flaws early, reducing manufacturing costs by 30% when they transitioned to mass production.
The Future of Prototype Injection Molds
The landscape of metal fabrication and injection molding is constantly evolving. With advancements in technologies such as:
- 3D Printing: Used for creating molds quickly and affordably.
- CAD Software: Enhanced design accuracy and efficiency.
- Innovative Materials: Expanding the possibilities for prototypes, even down to bio-based materials.
It’s clear that prototype injection molds will continue to play a pivotal role in product development, leading to faster design cycles and sustainable practices in manufacturing.
Conclusion: The Value of Prototype Injection Molds in Modern Manufacturing
In conclusion, prototype injection molds represent a fundamental component of the metal fabrication industry. They not only streamline the production process but also significantly enhance design accuracy, quality control, and overall operational efficiency. As businesses strive to innovate and reduce time-to-market, the role of these prototypes will become increasingly significant. For companies looking for a reliable partner in their prototyping needs, deepmould.net offers unparalleled expertise in delivering high-quality mold solutions tailored to your specific requirements.
For more detailed inquiries, don't hesitate to reach out through our website for custom solutions in prototype injection molds and other metal fabrication services.